王志玲1,2,王 正1(1.中国林业科学院木材工业研究所,北京市100091;2.济南大学化工学院山东省济南市250022)
前 言
胶粘剂用量的多少,已成为衡量一个国家、一个地区木材工业技术发展水平的重要标志。根据联合国粮农组织报道,2000年世界人造板的产量达到1.54亿立方米,耗用370万吨胶粘剂(以固体含量100%计)。据《中国林业统计资料》和已发表的有关数据推算,我国1997年木材胶粘剂用量为92万吨,预测2005年和2010年人造板用胶量将分别增至141万吨(干)和169万吨。人造板使用胶粘剂主要有脲醛树脂(UF)、酚醛树脂(PF)、三聚氰胺-甲醛树脂(MF),其中尤以UF用量大。
人造板工业的这三大胶种都使用甲醛作为原料之一。随着人们对安全意识和环保意识的增强,甲醛的释放越来越受到关注,同时也影响了人造板的销售。因此,开发环保型的胶粘剂,重点开发无甲醛或低游离甲醛型胶粘剂成为大势所趋。
异氰酸酯胶粘剂是首选胶种。
异氰酸酯胶粘剂自二战开始应用,并很快被人们喻为“可粘接任意物品的胶”。1951年,Dcppc最先用异氰酸酯胶接刨花板,1957年德国生产出第一批异氰酸酯刨花板。50多年来,对异氰酸酯胶粘剂的研究及应用已经有了长足的发展。在北美和欧洲,超过20%的OSB(定向结构板)及常规MDF(中密度纤维板)生产厂家使用MDI胶粘剂。MDI世界年产量超过150万吨。美国的道化学公司及亨斯公司,德国的拜尔公司及巴斯夫公司,日本的聚氨酯公司及三井公司的研究开发及生产应用均处于世界领先地位。
1 异氰酸酯胶粘剂的使用特点
异氰酸酯胶粘剂由于含有高反应活性的异氰酸酯基(-NCO),一方面可与木质及非木质纤维素原料如竹材、秸杆、棉杆等大分子中的羟基(-OH)化学键合,另一方面该胶粘剂还可以与水反应,它是人们寻找的唯一的既可以与人造板原料分子反应又可以与水反应的胶粘剂[5]。反应式如下所示(P表示木质或非木质原料):
P—OH+OCN—R—NCO→P—OCONH—R—NCO
P—OCONH—R—NCO+P—OH→P—OCONH—R—NHCOO—P
OCN—R—NCO+H20→[HOOC—NH—R—NH—COOH]—NH2—R—NH2+CO2nNH2—R—NH2+
nOCN—R—NCO→OCN—[R—NHCONH]n—NCOn>1—NH—COO—(氨基甲酸酯)将碎料分子有机地“桥接”起来,
—NH—CO—NH—(脲键)与—NH—COO—,在加热条件(大于100℃)下可进一步与游离的—NCO发生三维交联固化反应,使粘接强度进一步提高。并且—NH—COO—和—NH—CO—NH—都可与原料中纤维素等大分子形成氢键,使得原料大分子间相互缔合、缠绕更加牢固。它显示出传统三大胶种难以比拟的特点;高的粘接强度,短的热压时间,优异的耐水性、防潮性和耐侯性,低的用量,并彻底消除了甲醛排放的污染。但该胶并未获得广泛的商业接受,主要原因:
(1)价格问题 假设人造板异氰酸酯用胶量为4%,产品耗胶量为30kg/m3,单位价格以12元/kg计算,则产品胶成本为360元/m3;若用UF胶粘剂,用胶量为10%,产品耗胶量为150kg/m3,单位价格以1.5元/kg计,产品胶成本为225元/m3,二者相差甚远。
(2)对压板粘附问题 甲醛基胶粘剂通常不用脱膜剂,而异氰酸酯胶粘剂由于优良的粘接性能,热压时造成胶合板与台板粘合,因此,必须通过内或外脱膜剂的使用来解决这一问题,这也增加了产品的成本。
2 人造板用异氰酸酯胶粘剂的研究进展为解决上述问题,国内外科技工作者进行了卓有成效的研究,其方法主要有:
2.1 水乳化异氰酸酯法
以水为溶剂乳化异氰酸酯胶粘剂不仅可解决有机溶剂对环境的污染,而且有助于增加胶粘剂的体积,以便与纤维素原料达到更均匀地混合,为有效地防止异氰酸酯过多地与水生成聚脲,应尽可能地减少异氰酸酯胶与水的接触时间。在工业生产中,可采用间歇法在静态混合器中乳化,然后立即将原料涂胶;还可使水基脱膜剂、异氰酸酯胶、乳化剂及水进行在线乳化,这样既可最大限度地减少异氰酸酯胶与水反应,又实现了乳化及与脱膜剂的混合,可一举两得。
松坂康弘等提出在高压4~30MPa下,将两种液流喷射到混合器中混合和乳化,液流一是异氰酸酯,另一液流是反应性乳化剂及乳化介质。异氰酸酯包括MDI、TDI、HDI,PAPI等,PMDI是优选的。反应性乳化剂必须满足两个条件:一是可与异氰酸酯反应,另一个是起乳化作用。从原料成本和异氰酸酯化合物的相容性、发泡性能、产品板材的物理性能考虑,聚醚和聚酯多元醇是优选的,如聚氧乙烯烷基醚、聚氧乙烯烷基芳基醚、聚氧化乙烯山梨醇脂肪酸酯和氧化乙烯氧化丙烯的嵌段共聚物等。乳化介质可以是水、醇类(如甲醇、乙醇、丙醇)、烃类(如苯、甲苯和己烷)、极性溶剂(N,N-二甲基甲酰胺、N,N-二甲基乙酰胺和糠醛)或采用两种或两种以上的溶剂混合物,其中,从经济及安全的角度,水是优选的,使用水时,pH值可在1~13的范围内。为防止热压粘板,可加入脱膜剂,脱膜剂包括含8~28个碳原子的饱和/或不饱和脂肪族羧酸的金属和蜡,加入方法;可加入到乳化剂或乳化介质中。结果表明,连续压板50次,台板上无沉淀物,板材的物理性能优良。
美国专利US5744079公开了一种生产木质纤维素产品的胶粘剂,该胶由MDI或PMDI、熔点介于50~160℃蜡的水乳液、有机磷酸酯衍生物组成。C.J.莫里尔蒂等研究发现,将含较低二异氰酸酯含量的PMDI转变成水乳化形式,应用于人造板制造效果良好,PMDI最优选的是具有约35%(重量)或35%(重量)以下的二异氰酸酯的含量,降低二异氰酸酯含量的方法可通过蒸馏脱除某些二异氰酸酯,或将某些二异氰酸酯转变成三聚MDI,以此制成的人造板明显地降低成本,并具有优良的物理、机械性能。顾继友采用异氰酸酯(MDI、TDI、XDI、HDI、TMDI等)和经真空脱水后的多元醇类反应,于30~100℃,保温2~4h制得异氰酸酯基封端的预聚体,将此与一定浓度的乳化剂的水溶液、稳定剂的水溶液简单搅拌可制成异氰酸酯乳液胶粘剂,用该胶粘剂制得的木质、稻草及麦草刨花板各项物理性能均达到要求的指标。
2.2 无溶剂异氰酸酯预聚物法
为解决压板粘附问题,美国专利US4100328、US4609513公开了改进产品脱膜性能的异氰酸酯终端预聚体;为使用含水量较高的纤维素原料,美国专利US4546039公开了用MDI合成的预聚物,可用于含水量20%的木质纤维素碎料的涂布;美国专利US5002713公开了用含水量15%~40%的木质纤维素材料生产压塑制品的方法,在该专利中,使用了叔胺、有机金属催化剂或其混合物的催化剂,将疏水性异氰酸酯如PMDI及甲苯二异氰酸酯等加入到含催化剂的木质纤维素原料中,再将涂胶的原料热压成型。美国专利US4944823描述了异氰酸酯与碳水化合物反应的预聚物,碳水化合物可使用淀粉、糖等,生产上可将碳水化合物与液体二异氰酸酯混合后涂覆到木材上,然后压制成复合产品,这一方法有效并且价廉。
J.W.罗斯托泽成功地研究了采用多异氰酸酯与固体胺形成的反应性混合物作为胶粘剂。改进的胶粘剂的优点是使用少量价贵的多异氰酸酯即可获得与传统MDI可比的性能,固体胺既是扩链剂又起到液体胶粘剂的载体作用,结构上可以是脲、三聚氰胺或其混合物的干燥化合物,其成品成本与脲醛树脂相比具有可竞争性,该胶粘剂既可用于木质也可用于非木质纤维素原料如树皮、软木、甘蔗渣、秸杆、亚麻、竹子、稻壳、剑麻纤维和椰子纤维等。原料形状可以是颗粒、薄片、球状或粉末并可含占木质纤维素总重量1%~20%的水分。US4209433[、US4961795、US5217665和CN1330690公开了适合制备木质人造板的含多异氰酸酯和酚醛树脂的胶粘剂,酚醛树脂是可熔性的,这些胶粘剂不含有机溶剂,并且不需要催化剂固化,其固化温度比单独使用酚醛树脂低,与通常含水的可溶性酚醛树脂比,压制过程中,没有多余的水必须除去,因此缩短了固化时间,耐水性比单独用酚醛树脂好,因使用了较少的异氰酸酯,从而导致成本降低,并且该胶粘剂热压粘板的程度同时下降。
3 发展趋势
由诸多的研究及应用可看出,以PMDI及水乳化的PMDI(EMDI)应用最多。Galbraith报道EMDI比PMDI更有效,而Jones[21]报道EMDI不比PMDI好。Napadopouios[3]将PMDI和EMDl分别用于刨花板胶合,并测试主要力学性能,测试结果见表1。
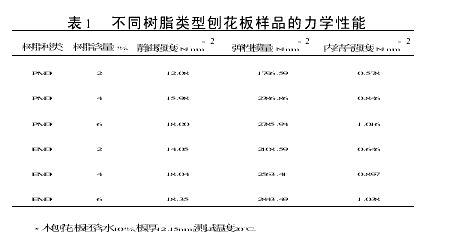
由上表可看出,用胶量相同时,EMDI胶合刨花板各项性能均优于用PMDI。用2%EMDI胶合的三项力学性能接近于用4%PMDI。这可能是因为EM DI与原料混合比表面积大,反应生成的互穿网络结构更充分。我国在水乳型异氰酸酯胶粘剂研究上多以异氰酸酯与聚醚多元醇加聚反应生成预聚体,在预聚体分子链中引入亲水基团,再用二元醇或二元胺与链端的异氰酸酯基反应封端,生成少支链的线形聚合物,然后加水乳化。该法制得的胶粘剂颗粒较细且分布均匀,具有较好的储存稳定性,但在分子链中亲水基团的引入,使得胶层耐水性、耐热性、粘接强度不理想。因此对水性异氰酸酯胶粘剂改性的研究十分活跃,但成功用于生产报道较少,成功用于人造板复合的报道则更少。究起原因,主要是因为异氰酸酯胶大分子中不再含有与木质或非木质大分子中羟基(—OH)反应的活性异氰酸酯基,因此胶合后, 是与原料基材存在着分子间的作用力,难以满足粘接强度等性能上的要求。所以,应采取措施,有效地保留活性异氰酸酯基(—N=C=O),如将异氰酸酯胶、水、乳化剂混合乳化后立即将碎料涂胶,即在线乳化;或通过加入加速交联的微胶囊化固化剂,热压时与异氰酸酯基交联固化。这可能给研究者和生产者一个惊喜。 |